Полиуретановые эластомеры и все, что нужно о них знать
Эластомеры — это высокоэластичные полимеры, способные многократно удлиняться и возвращаться к первоначальному размеру. Полиуретановые эластомеры получают путем удлинения цепей форполимера, состоящего из диола и диизоцианата.
Обладают исключительными физико-механическими свойствами. По своим качественным показателям они не уступают металлическим, пластиковым и превосходят резиновые изделия. Если сравнивать полиуретан — резину, то полиуретан показывает лучшие результаты по:
- эластичности — относительное удлинение при разрыве полиуретана в два раза больше;
- прочности — прочность в два раза выше;
- устойчивости к истиранию — износостойкость полиуретана в три раза больше;
- высокая твердость позволяет применять его вместо металла там, где существуют высокие механические нагрузки;
- изделия из полиуретана оказываются легче металлических аналогов, поэтому затраты энергии, направленные на их вращение, составляют меньшую величину
- стойкость к повышенному давлению делает возможным использование для производства манжет, колец, втулок, вкладышей, сальников высокой прочности;
- ПУ имеет низкую теплопроводность. Полиуретан сохраняет упругость при отрицательных температурах до -50 °C. Также работает при температурах до +110 °C и даже может выдержать непродолжительное увеличение температуры до +140 °C;
- из-за стойкости к воздействию бензина, масел полиуретановые колеса более предпочтительны по сроку эксплуатации, чем каучуковые и резиновые. Также по сроку службы выигрывают полиуретановые уплотнения;
- полиуретаны – диэлектрики, поэтому полиуретановое покрытие обеспечивает не только водо-, термо- , но и электроизоляцию;
- химическая неактивность, стойкость к возникновению плесени, микроорганизмам делает предпочтительным эксплуатацию в пищевой промышленности, медицине;
- полиуретановые листы, втулки, стержни, другие изделия способны подвергаться многократным деформациям без изменения прочностных свойств. Большой срок эксплуатации, надежность делают такую продукцию более востребованной, в сравнении с резиновыми аналогами.
Рассмотрим некоторые типы полиуретановых эластомеров
1. Литьевые полиуретаны
Литьевые материалы получают полимеризацией простого или сложного высокомолекулярного полиола, ароматического диизоцианата и удлинителя цепи. Литьевые материалы получают обычно при высокой температуре в одну стадию.
2. Вальцуемые полиуретаны
Получают при небольшом количестве диизоцианата, в результате чего происходит поперечное сшивание. Продукт представляет собой мягкий каучук, который можно перерабатывать на вальцах подобно другим эластомерам. Свойства конечного продукта похожи на литьевые, однако диапазон свойств сильно ограничен. Используется, когда форма или размер изделия не позволяет использовать его литьевым способом.
3. Термопластичные полиуретаны
По химическому составу похожи на литьевые эластомеры, а для поперечной сшивки обычно используется избыток диизоцианата. По свойствам схож на нейлон, а основным преимуществом является возможность литья при высокой температуре.
4. Ячеистые полиуретаны
Рассматриваются как более эластичные и мягкие полиуретановые эластомеры с плотностью 0,35-0,65 г/см3, их нельзя сравнивать с обычными пенополиуретанами.
Применение полиуретановых эластомеров
Полиуретановые продукты широко распространены на промышленном рынке благодаря широкому спектру прочностных характеристик. Эти материалы вытеснили изделия из резины, так как их можно эксплуатировать в агрессивных средах, при больших динамических нагрузках и в более широком диапазоне температур. Спектр рабочих температур для данного материала составляет соответственно -60 °C — +110 °C. Наиболее часто применяются в машиностроении, обувной промышленности, колесах и массивных шинах, гидравлических уплотнениях, одежде из волокон спандекса и др.
На рынке промышленности полиуретан чаще всего представлен в виде твердых заготовок (листов, стержней). Но используются и более мягкие — вспененные формы полиуретана, а также материал в жидком виде.
Образование эластомеров
Влияние полиэфира
Как упоминалось выше, полиуретановые литьевые эластомеры получаются полиаддитивным методом из диизоцианатов и полиолов. Этот метод неоднократно описан. Применяются, главным образом, такие изоцианаты, как метилендифенилдиизоцианат (МДИ) и ТДИ, а в качестве полиольного компонента используются сложные и простые полиэфиры. Именно полиэфиры вносят “мягкий сегмент” и придают эластичность продукту. За основу чаще всего используют линейный простой полиэфир с молекулярным весом 400-7000 г/моль. Чем ниже молекулярный вес, тем жестче будет эластомер. Так происходит из-за того, что увеличивается концентрация уретановых групп. Стандартным простым полиэфиром для изготовления эластомеров является политетраметиленгликоль ( РТМЕГ), который придает эластомерам исключительные физико-механические свойства, включая низкую истираемость. Преполимеры на основе полипропиленгликолей по механическим свойствам уступают РТМЕГ за счет присутствия боковых метильных групп, которые препятствуют образованию связей между полярными уретановыми группами. Так что полиуретаны, полученные из таких полиэфиров, имеют худшее сопротивление разрыву и напряжение. При снижении молекулярного веса ППГ свойства его обычно ухудшаются, но несмотря на перечисленные недостатки ППГ представляет большой интерес для производства благодаря низкой стоимости.
К сложным полиэфирам, наиболее широко используемым в настоящее время в производстве эластомеров, относят полиэтиленадипинат, но представляют интерес и смешанные полиэфиры типа полиэтиленпропиленадипината. Эластомеры на основе сложных полиэфиров отличаются высокой прочностью в сочетании с эластичностью, маслостойкостью и стойкостью к кислотам и щелочам.
Диизоцианаты
Диизоцианаты за счет уретановых и ароматических групп привносят в систему “жесткий сегмент” и увеличивают показатель прочности и напряжения. В производстве литьевых эластомеров использую три основных вида диизоцианатов: НДИ, ТДИ и МДИ. Для производства вальцуемых полиуретанов применяются только ТДИ и МДИ, а в производстве термопластичных полиуретанов единственным диизоцианатом, используемым в широких масштабах, является МДИ. В производстве в основном используется ТДИ 80/20, который представляет собой смесь 2,4-; 2,6-изомеров. ТДИ-преполимеры обладают низкой реакционной способностью. Для увеличения реакционной способности ТДИ-преполимеров проводят реакцию с ароматическими диаминами. В результате получаются полимочевинные связи, которым эластомеры обязаны своими свойствами. Реакционная способность МДИ-преполимеров, напротив, так высока, что возможность проведения реакции с алифатическими или ароматическими диаминами в условиях производства затруднительна. Эти компоненты реагируют в течение нескольких секунд, поэтому такие реакционные смеси не пригодны для способа заливки в форму при низком давлении. Поэтому для преобразования МДИ-преполимеров используют сшиватели на основе гликолей, как правило, бутандиол.
У МДИ-преполимеров - сравнительно узкий диапазон переработки. Поэтому необходимо очень точно придерживаться рекомендованных параметров производственного процесса, таких как температура продукта, настройки литьевой машины, температура пресс-форм, так как они сильно влияют на результат. В зависимости от веса и геометрии детали могут формироваться различные температуры по поверхности детали. У небольших деталей, имеющих тонкие стенки, а также у деталей с низкой жёсткостью, реакция может идти быстрее. Таким образом благодаря более высокой температуре реакционной массы или пресс-формы обеспечивается экономичное производство. При получении крупных и толстостенных или чрезвычайно жёстких деталей выделяется много тепла благодаря экзотермической реакции. Скорость реакции здесь очень высокая, однако из-за высоких температур в формованной детали наблюдаются усадка, образование трещин и пр. Поэтому при производстве крупных деталей понижают температуру реакционной массы и/или пресс-формы. Настройки параметров рабочего процесса для детали весом 500 граммов кардинально отличаются от настроек для деталей с другим весом, например, 2 кг. Узкий диапазон переработки даже частично визуально заметен на готовом продукте: поверхность извлечённой из формы детали матовая, в худшем случае выглядит неоднородной.
В отличие от этого, сшивание ТДИ-преполимеров аминами обеспечивает очень широкий диапазон переработки: различия в настройках рабочих параметров, в температуре форм, температуре или соотношении смешивания, вплоть до неполного смешивания не так велики и не всегда отражаются на внешнем виде готовой детали. Производитель не может недооценить это преимущество. Готовые эластомерные детали из ТДИ-преполимеров, прошитых аминами, имеют блестящую чистую поверхность. Поэтому системы на основе ТДИ-преполимеров, сшиваемые аминами, считаются простыми в переработке (easy-to-process-systems).
Диамины
Традиционный диаминный сшиватель 3,3'-дихлор-4,4'-диаминодифенилметан (МОСА) обеспечивает высокий уровень свойств полиуретановых эластомеров. Однако он представляет собой кристаллическое вещество с высокой температурой плавления (105°С), что создает трудности при его переработке. Пары МОСА при температуре выше 100°С над расплавом имеют высокую токсичность. Для перевода МОСА в жидкое состояние при температуре ниже 100°С могут быть использованы полиэфиры, низкомолекулярные диолы, пластификаторы.
Известен жидкий отвердитель для форполимеров с концевыми изоцианатными группами, включающий ароматический диамин МОСА и нелетучий растворитель политетраметилен-оксиддиол. Недостатком жидкого отвердителя данного состава является то, что полиуретановые изделия с его содержанием, эксплуатирующиеся в режиме циклического нагружения при значительной деформации, имеют невысокий ресурс - количество циклов нагружения до разрушения материала. Кроме того, такой отвердитель плохо смешивается с форполимерами на основе неполярных олигодиендиолов, что ограничивает возможности его применения. При использовании пластификаторов тоже могут возникнуть ряд трудностей, так как некоторые из них обладают заметной летучестью, что резко ограничивает возможности его применения в изделиях, эксплуатирующихся на открытом воздухе при положительных температурах. Испарение пластификатора приводит к нестабильности и неоднородности свойств материала по толщине изделия.
Классическим жидким ароматическим диамином является диметилтиотолуолдиамин (ДМТДА) или Ethancure 300. Основним преимуществом такого диамина является низкая токсичность. Используется как для горячего, так и для холодного литья при комнатной температуре. Жидкие диаминные отвердители обладают долгим временем жизни, поэтому являются незаменимыми отвердителями для полиуретановых литьевых эластомеров. Типичные области применения эластомеров холодного отверждения – это изготовление эластичных форм, получение полиуретана в полевых условиях, изготовление защитно-декоративных покрытий.
Время жизнеспособности смеси
Основным недостатком ароматических диаминных отвердителей (типа мока) является большая скорость гелеобразований композиций, что затрудняет их технологическую переработку. При использовании гликольных отверждающих агентов гелеобразование происходит медленнее, а показатели физико-механических свойств продуктов хуже, чем при использовании аминных отвердителей. Комбинируя аминные и гликольные отвердители, получают продукты с требуемыми свойствами. Лучшими из гликольных отвердителей являются низкомолекулярные диолы. Скорость реакции отверждения эластомеров также зависит от полиуретановой композиции и температуры отверждения. При температуре 85-150°С процесс отверждения протекает достаточно быстро. Также, чтобы увеличить жизнеспособность литьевых полиуретановых композиций и повысить технологичность их переработки, преполимер и структурирующий агент растворяют в органических растворителях и пластификаторах. Отверждение покрытий проводят при температуре 100°С в течение 30-35 мин.
Время полного отверждения ненаполненных эластомерных композиций - 3-5 дней. Применение катализаторов и нагревание композиций ускоряет процесс отверждения. Обычно используют металлоорганические катализаторы, в частности на основе октоата олова или дибутилдилаурата олова. Классическими катализаторами являются; Dabco T-120, Cosmos 19, Dabco T-9, Cosmonate LL. Катализатор, содержащий диазобициклооктан является эффективным при температуре 20-75°С. Дибутилдилаурат олова отверждает композицию при температуре 100-125°С в течение 30-45 мин. Однако следует отметить, что частичное отверждение эластомерных композиций протекает в течение нескольких минут; дальнейшее отверждение может происходить в складском помещении при комнатной температуре.
Другие Статьи
Смотреть все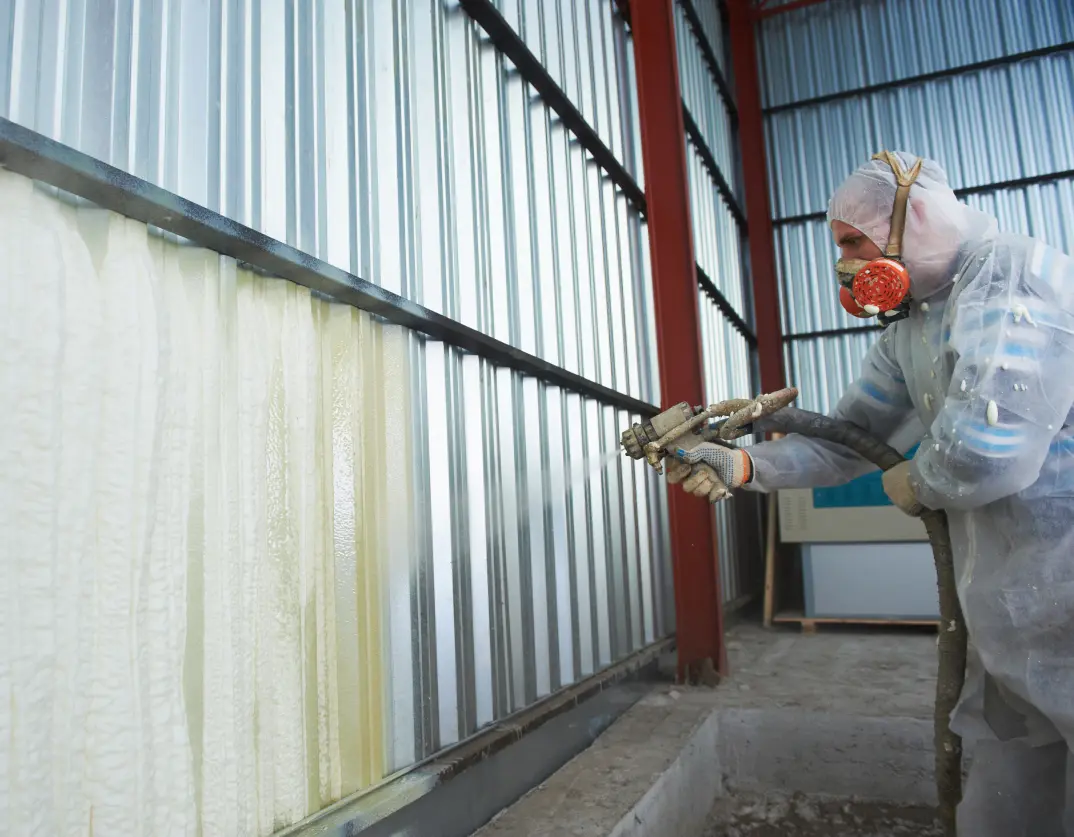